Unequal I/H Section Calculator
This tool calculates the properties of an I/H section, with unequal flanges (also called unequal I beam or unequal double tee). Enter the shape dimensions below. The calculated results will have the same units as your input. Please use consistent units for any input.
h = | |||
tw = | |||
bu = | |||
tu = | |||
bd = | |||
td = | |||
Geometric properties: | |||
Area = | |||
Perimeter = | |||
hw = | |||
yc = | |||
Properties related to x-x axis: | |||
Ix = | |||
Sx = | |||
Zx = | |||
ypna = | |||
Rgx = | |||
ADVERTISEMENT | |||
Properties related to y-y axis: | |||
Iy = | |||
Sy = | |||
Zy = | |||
Rgy = | |||
Other properties: | |||
Iz = | |||
![]() |
ADVERTISEMENT
Theoretical background
Table of contents
Geometry
The area A and the perimeter P of a double-tee, with unequal flanges, can be found by the next two formulas:
The clear height of the web, that appears in above formulas, is the clear distance between the two flanges:
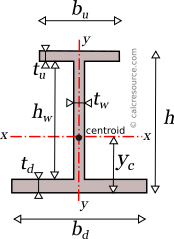
Due to symmetry, around the y axis, the centroid of the cross-section must lie on the y axis too. Therefore, . However, the same cannot be said for the other axis (x-x) since no symmetry exists around it, due to the unequal flanges. The exact location of the centroid should be therefore calculated. To find its distance, , from a convenient axis of reference, say the lower edge of the cross-section, the first moments of area, of the web and the two flanges, relative to the same edge are employed (note: the first moment of area is defined as the area times the distance of the area centroid from the axis of reference). That is:
where
- , is the area of the lower flange
- , is the area of the upper flange,
- , is the area of the web,
- , is the distance of the lower flange centroid from the bottom edge,
- , is the distance of the upper flange centroid from the bottom edge,
- , is the distance of the web centroid from the bottom edge.
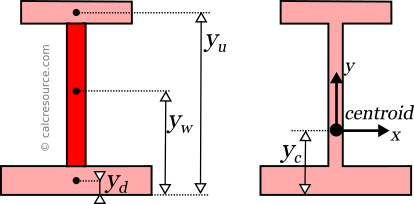
From the last expression, the location of the centroid can be calculated directly, as:
Moment of Inertia
Major axis
Similarly, in order to find the moment of inertia of an unequal I beam, the total cross-section is divided into three, smaller ones, one for the lower flange, one for the upper one and one for the web. Therefore, the moment of inertia ,relative to centroidal x-x axis, is determined like this:
where,
- , the moment of inertia of the lower flange relative to the centroidal x-x axis,
- , the moment of inertia of the upper flange relative to the centroidal x-x axis,
- , the moment of inertia of the web relative to the centroidal x-x axis.
For each of the above expressions the so called 'parallel axis theorem' has been employed for the estimation of the respective moments of inertia of the three parts. For more information about this technique, check here.
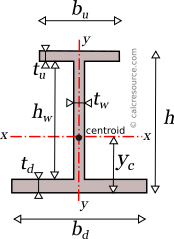
Minor axis
Again, the total cross area is divided into three parts, one for the lower flange, one for the upper one and one for the web. This time however, the axis of bending (y-y) is also an axis of symmetry (for all three parts), and therefore the calculations are a bit easier (because the use of the parallel axis theorem is unnecessary). The total moment of inertia is found as:
where,
- , the moment of inertia of the lower flange relative to the centroidal y axis,
- , the moment of inertia of the upper flange relative to the centroidal y axis,
- , the moment of inertia of the web relative to the centroidal y axis,
Polar
The polar moment of inertia, describes the rigidity of a cross-section against torsional moments, whereas the planar moments of inertia described above, are related to flexural bending. The calculation of the polar moment of inertia around an axis z (perpendicular to the section), can be done with the Perpendicular Axes Theorem:
where the and are the moments of inertia around axes x and y that are mutually perpendicular with z and meet at a common origin.
Applications
The moment of inertia (second moment or area) is used in beam theory to describe the rigidity of a beam against flexure. The bending moment M applied to a cross-section is related to its moment of inertia, with the following equation:
where E is the Young's modulus, a property of the material, and , the curvature of the beam due to the applied load. Therefore, it can be seen from the former equation, that when a certain bending moment M is applied to a beam cross-section, the developed curvature is reversely proportional to the moment of inertia I.
The dimensions of moment of inertia are .
Elastic section modulus
The elastic section modulus of any cross section around axis x (centroidal), describes the response of the section under elastic flexural bending. It is defined as:
where the moment of inertia of the section around x axis and Y the distance of a section fiber (typically the most distant one), from the same x axis. Because the unequal I beam is unsymmetrical around x axis, the distance Y should be different for the upper and bottom fiber of the section. As a result, two different section moduli could be calculated. Typically, the smaller one is of interest (the one corresponding to bigger Y), because it is related with the more stressed fiber, as explained later in this section.
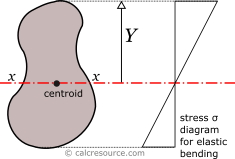
Similarly, the section modulus , around y axis, which, for the unequal I beam, happens to be symmetry axis too, is written as:
where the moment of inertia of the section around y axis and , the distance of a side edge fiber from the same y axis. This time however, the distance X is the same for the left and right fibers of the cross-section and equal to .
Elastic bending stress
If a bending moment is applied on axis x, the section will respond with normal stresses, varying linearly with the distance from the neutral axis (which under elastic regime coincides to the centroidal x axis). Along neutral axis the stresses are zero. Absolute maximum will occur at the most distant fiber, with magnitude given by the formula:
From the last equation, the section modulus can be considered for flexural bending, a property analogous to cross-sectional A, for axial loading. For the latter, the normal stress is F/A.
The dimensions of section modulus are .
Plastic section modulus
The plastic section modulus is similar to the elastic one, but defined with the assumption of full plastic yielding of the cross section due to flexural bending. In that case, the whole section is divided in two parts, one in tension and one in compression, each under uniform stress field. For materials with equal tensile and compressive yield stresses, this leads to the division of the section into two equal areas, in tension and in compression, separated by the neutral axis. This is a result of equilibrium of internal forces in the cross-section, under plastic bending. Indeed, the compressive force would be , assuming the yield stress is equal to , in compression, and that the material over the entire compressive area has yielded (thus the stresses are equal to everywhere). Similarly, the tensile force would be , using the same assumptions. Enforcing equilibrium:
The axis is called plastic neutral axis, and for non-symmetric sections, is not identical to the elastic neutral axis (which again is the centroidal one). The unequal I/H section, is indeed non symmetric around strong axis (x axis). As a result, the plastic neutral axis of an unequal I-beam, for strong axis flexure, does not pass through centroid.
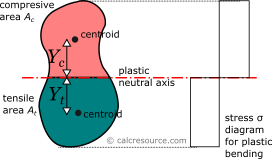
Around strong axis
For an unequal I-beam, the x axis, that is parallel to flanges, is typically the strong axis of the cross-section. Since the plastic neutral axis divides the cross-section to equal areas, it must be:
The above expression can be utilized for the calculation of the position of the neutral axis. First, let's assume that the plastic neutral axis, has a distance equal to from the lower edge. Also, let's assume that it is located somewhere between the two flanges. In mathematical terms:
This is just an assumption. Even though, it seems intuitive for the plastic neutral axis to be located between the two flanges, this is not always the case. It really depends on the relative sizes of the two flanges. Nevertheless, let's consider that the above assumption is true for the moment. The half sectional area, below the plastic neutral axis should be:
The only unknown is . Rearranging the equation we get:
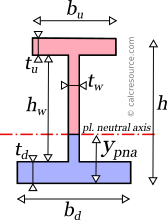
The last expression allows the calculation of the plastic neutral axis distance from the lower edge, provided our initial assumption is valid. It is easy to find the right conditions for this to happen. Substituting the calculated , to the assumed inequality we get:
where , is the area of the lower flange and , the area of the upper flange. The above inequality is equivalent to the following two inequalities being both true:
In other words, the plastic neutral axis is located between the flanges of the unequal I beam section, if neither of the two flanges takes more than half of the total sectional area.
Following, the calculation of , the centroids of the two areas at either sides of the neutral axis can be found and the evaluation of the plastic modulus becomes straightforward. The following formula is derived for the plastic modulus:
A similar procedure should be followed, when the plastic neutral axis passes through a flange, either the lower or the upper one. If it passes through the lower flange (should occur when that flange has more than half of total sectional area, i.e. ), the following formula is derived, for the plastic modulus:
where:
- ,
- ,
- ,
- .
Finally, if the plastic neutral axis passes through the upper flange (should occur when that flange has more than half of total sectional area, i.e. ), the following formula is derived, for the plastic modulus:
where:
- ,
- ,
- ,
- .
Around weak axis
For the unequal I-beam, the y axis, that is perpendicular to flanges, is typically the weak axis. This is also an axis of symmetry for the cross-section. As a result, the plastic neutral axis, this time, needs no calculations. It is identical to the centroidal y axis. Also, the plastic modulus is much easier to evaluate. Three rectangular areas are contributing to it, all symmetrically positioned around the y axis: two areas for the flanges and one for the web. The following formula is derived:
Plastic bending
The plastic modulus is related to the stresses of a cross-section under bending in the plastic regime, in an analogous manner the elastic modulus does for the elastic regime. If a bending moment is applied around axis x, and the entire section becomes fully plastified, so that every fiber has reached yield stress of the material, , then the following formula is valid:
From the last equation, the bending moment that causes full yield of the cross-section, typically named plastic moment, can be determined .
The dimensions of plastic modulus are .
Radius of gyration
Radius of gyration of a cross-section, relative to an axis, is given by the formula:
where I the moment of inertia of the cross-section around the same axis and A its area. The dimensions of radius of gyration are . It describes how far from centroid the area is distributed. Small radius indicates a more compact cross-section. Circle is the shape with minimum radius of gyration, compared to any other section with the same area A.
Unequal I/H section formulas
The following table, lists the main formulas, related to the mechanical properties of the unequal I beam section (also called double-tee section).