Circular Section Calculator
This tool calculates the properties of a circular cross-section. Enter the circle radius R or the diameter D, below. The calculated results will have the same units as your input. Please use consistent units for any input.
R = | |||
or... | |||
D = | |||
Geometric properties: | |||
Area = | |||
Perimeter = | |||
Properties related to any centroidal axis: | |||
I = | |||
S = | |||
Z = | |||
Rgx = | |||
Iz = | |||
ADVERTISEMENT |
![]() |
ADVERTISEMENT
Definitions
Table of contents
Geometry
The area A and the perimeter P, of a circular cross-section, having radius R, can be found with the next two formulas:
Moments of Inertia
The moment of inertia (second moment of area) of a circular section around any axis passing through its centroid, is given by the following expression:
where R the radius of the section.
Equivalently, the moment of inertia is given, in terms of circle diameter , by the formula:
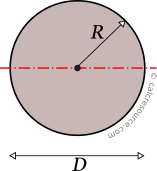
Elastic bending and moment of inertia
The moment of inertia (second moment or area) is used in beam theory to describe the rigidity of a beam against flexure. The bending moment M applied to a cross-section is related with its moment of inertia with the following equation:
where E is the Young's modulus, a property of the material, and , the curvature of the beam due to the applied load. Therefore, it can be seen from the former equation, that when a certain bending moment M is applied to a beam cross-section, the resulting curvature is reversely proportional to the moment of inertia I.
Polar moment of inertia
The polar moment of inertia, describes the rigidity of a cross-section against torsional moment, likewise the planar moments of inertia described above, are related to flexural bending. The calculation of the polar moment of inertia around an axis z (perpendicular to the section), can be done with the Perpendicular Axes Theorem:
where the and are the moments of inertia around axes x and y, which are mutually perpendicular with z and meet at a common origin. Since, for a circular section it is: , the above equation becomes:
The dimensions of moment of inertia are .
Elastic modulus
The elastic section modulus of any cross section around axis x (centroidal), describes the response of the section under elastic flexural bending. It is defined as:
where , the moment of inertia of the section around x axis and Y the distance from centroid of a section fiber, parallel to the axis. Typically, the most distant fibers are of particular interest. For the circle, the bigger distance from center is . Therefore, application of the above formula to a circular cross-section, provides the following expression, for the elastic modulus, around any centroidal axis:
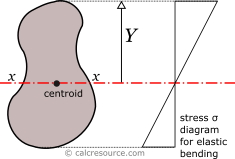
Elastic stresses
If a bending moment is applied around axis x, the section will respond with normal stresses, varying linearly with the distance from the neutral axis (which under elastic regime coincides to the centroidal x-x axis). Along neutral axis the stresses are zero. Absolute maximum will occur at the most distant fiber, with magnitude given by the formula:
From the last equation, the section modulus can be considered for flexural bending, a property analogous to cross-sectional A, for axial loading. For the latter, the normal stress is F/A.
The dimensions of section modulus are .
Plastic modulus
The plastic section modulus is similar to the elastic one, but defined with the assumption of full plastic yielding of the cross section due to flexural bending. In that case the whole section is divided in two parts, one in tension and one in compression, each under uniform stress field. For materials with equal tensile and compressive yield stresses, this leads to the division of the section into two equal areas, , in tension and , in compression, separated by the neutral axis. This is a result of equilibrium of internal forces in the cross-section, under plastic bending conditions. Indeed, the internal compressive force, over the entire compressive area, would be , assuming full plastification (i.e. the material would have yielded everywhere) and that the compressive yield stress is equal to (ignoring any plastic hardening in this context). Similarly, the internal tensile force would be , using the same assumptions. Enforcing equilibrium:
The axis is called plastic neutral axis, and for non-symmetric sections, is not the same with the elastic neutral axis (which again is the centroidal one). The circular section however, is a symmetrical one and therefore the plastic neutral coincides with the elastic one. In other words, the plastic neutral axes passes through the center of the circle.
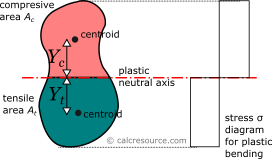
The plastic modulus, for flexural bending around a given axis, is given by the general formula:
where , the distance of the centroid of the compressive area from the plastic neutral axis and the respective distance of the centroid of the tensile area.
For the case of a circular cross-section, the plastic neutral axis passes through centroid, as already mentioned, dividing the whole area into two equal parts. The compressive area would be a semicircle, with area . Its centroid lies at a distance equal to , from the axis (check our centroids table for reference). Due to symmetry, the same applies for the tensile area, too. Therefore, the plastic section modulus, of the circular section, is found like this:
which is simplified to:
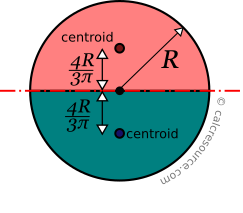
Radius of gyration
Radius of gyration of any cross-section, relative to an axis, is given by the general formula:
where I the moment of inertia of the cross-section around the same axis and A its area. The dimensions of radius of gyration are . It describes how far from centroid the area is distributed. Small radius indicates a more compact cross-section. For a circular section, substitution to the above expression gives the following radius of gyration, around any axis, through center:
Circle is the shape with minimum radius of gyration, compared to any other section with the same area A.
Circular section formulas
The following table, includes the formulas, one can use to calculate the main mechanical properties of the circular section.
Circular section properties![]() | |
---|---|
Quantity | Formula |
Area: | |
Circumference: | |
Moment of inertia: | |
Elastic modulus: | |
Plastic modulus: | |
Radius of gyration: | |
Approximations: |